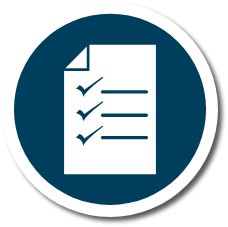
Inspections
An inspection is an examination of a workplace, selected work area and/or specific hazards, machinery, tools, equipment and/or work practices. Inspection findings are compared to applicable standards. Standards may be established by legislation, manufacturers, employers or industry best practices. The underlying (root) cause(s) of any deficiencies/hazards are determined and corrective actions prioritized according to risk. Corrective actions are assigned target dates for implementation.
Effective inspections are a proactive activity to improve workplace health and safety. By identifying hazards before they cause an incident and addressing the root causes, the workplace can prevent injuries and illnesses, and the associated costs (both human and financial).
Inspections also provide an opportunity to communicate with workers and follow up on hazard controls to determine if they have been implemented as intended and are effective. Effective inspections create a positive safety experience by proactively identifying and addressing hazards and by recognizing good health and safety practices.
Inspections may be informal or formal. Some inspections are prescribed under legislation.
An employer should:
- Identify:
- the types of inspections to be conducted (for example: regular planned workplace inspections, equipment inspections, special inspections such as after an incident)
- the areas/sites to be inspected
- the equipment to be inspected
- the work activities to be inspected
- Develop employer specific inspection checklists that:
- specify the work area to be inspected
- list hazards that should be inspected
- list hazardous activities that should be inspected
- identify standards to measure workplace conditions against
- identify standards such as standard operating procedures to measure workplace actions against
- Develop schedules for inspection completion
- Assign personnel to conduct inspections
- Train personnel assigned to conduct inspections
- Conduct inspections as scheduled
- Develop a process to verify corrective actions are implemented
- Communicate inspection results
- Maintain records of inspections
- Review inspection processes regularly. As a workplaces changes, the hazards and the controls may change
The following legislation is not all inclusive. You are responsible for knowing and complying with all legislation applicable to your place of employment. Please refer to the original legislation to find out exactly what requirements apply to your business. WorkSafe Saskatchewan does not offer any advice as to your obligations under any applicable legislation, and assumes no responsibility or liability for your obligations under the applicable legislation.
You can download copies of legislation for free from http://www.publications.gov.sk.ca/legislation.cfm.
Occupational Health and Safety Regulations, 2020
PART 3
General Duties
Occupational health and safety program
3‑11(1). Subject to subsection (2), an occupational health and safety program required by section 3‑20 of the Act must include:
(a) a statement of the employer’s policy with respect to the protection and maintenance of the health and safety of the workers;
(b) the identification of existing and potential risks to the health or safety of workers at the place of employment and the measures, including procedures to respond to an emergency, that will be taken to reduce, eliminate or control those risks;
(c) the identification of internal and external resources, including personnel and equipment, that may be required to respond to an emergency;
(d) a statement of the responsibilities of the employer, the supervisors and the workers;
(e) a schedule for the regular inspection of the place of employment and of work processes and procedures;
(f) a plan for the control of any biological or chemical substance handled, used, stored, produced or disposed of at the place of employment and, if appropriate, the monitoring of the work environment;
(g) a plan for training workers and supervisors in safe work practices and procedures, including any procedures, plans, policies or programs that the employer is required to develop pursuant to the Act or any regulations made pursuant to the Act that apply to the work of the workers and supervisors;
(h) a procedure for the investigation of accidents, dangerous occurrences and refusals to work pursuant to section 3‑31 of the Act at the place of employment;
(i) a strategy for worker participation in occupational health and safety activities, including audit inspections and investigations of accidents, dangerous occurrences and refusals to work pursuant to section 3‑31 of the Act; and
(j) a procedure to review and, if necessary, revise the occupational health and safety program at specified intervals that are not greater than 3 years and whenever there is a change of circumstances that may affect the health or safety of workers.
(2) The places of employment set out in Table 7 of the Appendix with 10 or more workers are prescribed for the purposes of section 3‑20 of the Act.
(3) An employer at a place of employment mentioned in subsection (2) shall establish an occupational health and safety program that meets the requirements set out in subsection (1).
Examination of plant
3‑12. An employer, contractor or owner shall:
(a) arrange for the regular examination of any plant under the control of the employer or owner to ensure, to the extent that is reasonably practicable, that the plant is capable of:
(i) withstanding the stress likely to be imposed on the plant; and
(ii) safely performing the functions for which the plant is used; and
(b) as soon as is reasonably practicable, correct any unsafe condition found in the plant and take immediate steps to protect the health and safety of any worker who may be at risk until the unsafe condition is corrected.
Boilers and pressure vessels
3‑15. An employer, contractor or owner shall ensure that any boiler or pressure vessel used at a place of employment that is not required to be inspected or registered pursuant to The Boiler and Pressure Vessel Act, 1999 is properly constructed and maintained.
Inspection of place of employment
3‑17(1). An employer, contractor or owner shall allow members of a committee or a representative to inspect a place of employment at reasonable intervals determined by the committee or the representative and employer.
(2) On written notice by the committee or the representative of an unsafe condition or a contravention of the Act or any regulations made pursuant to the Act, the employer, contractor or owner shall:
(a) take immediate steps to protect the health and safety of any worker who may be at risk until the unsafe condition is corrected or the contravention is remedied;
(b) as soon as possible, take suitable actions to correct the unsafe condition or remedy the contravention; and
(c) inform the committee or the representative in writing of:
(i) the actions that the employer, contractor or owner has taken or will take pursuant to clause (b); or
(ii) the employer’s, contractor’s or owner’s reasons for not taking action if the employer, contractor or owner has not taken any actions pursuant to clause (b).
PART 4
Committees and Representatives
Minutes
4‑5(1). A committee shall:
(a) record minutes of each meeting in a format provided by the ministry and keep the minutes on file with the committee;
(b) post a copy of the minutes at a location that is readily accessible to workers at the place of employment until all concerns recorded in the minutes are resolved.
(2) The employer shall maintain a copy of the minutes and have them readily available for inspection by a committee member or an occupational health officer.
Opportunity for necessary activities
4‑11(1). An employer or contractor shall ensure that:
(a) the members of a committee or a representative are allowed to examine any log book, inspection report or other record that the employer or contractor is required to keep at the place of employment pursuant to the Act or any regulations made pursuant to the Act;
(b) members of a committee or a representative have reasonable opportunity, during normal working hours and without loss of pay or other benefits, to receive and investigate concerns, to inform workers of the provisions of the Act or any regulations made pursuant to the Act or to conduct other business proper to the functioning of the committee or the representative;
(c) members of a committee have reasonable opportunity to hold a special meeting pursuant to section 4‑7 at any time; and
(d) a representative has reasonable opportunity to hold a special meeting pursuant to subsection 4‑10(2) at any time.
(2) An employer or contractor shall ensure that no member of a committee or representative who participates in a regular meeting held pursuant to section 4‑4 or subsection 4‑10(1) or in a special meeting held pursuant to section 4‑7 or 4‑12 or subsection 4‑10(2) loses any pay or other benefits as a result of that participation.
PART 5
First Aid
First aid register
5‑8. An employer or contractor shall ensure that:
(a) each first aid station is provided with a first aid register;
(b) all particulars of the following are recorded in the first aid register:
(i) each first aid treatment administered to a worker while at work;
(ii) each case referred for medical attention;
(c) a first aid register is readily available for inspection by the committee or representative; and
(d) a first aid register no longer in use is retained at the place of employment for a period of not less than 5 years from the day on which the register ceased to be used.
PART 7
Personal Protective Equipment
Respiratory protective devices
7‑3(1). If a worker is likely to be exposed to dust, fumes, gas, mist, aerosol or vapour or any airborne contaminant that may be present in any amounts that are harmful or offensive to the worker, an employer or contractor shall:
(a) provide an approved respiratory protective device for use by the worker that:
(i) provides suitable and adequate protection to the worker from one or more airborne contaminants;
(ii) is the proper size for the worker’s face;
(iii) if a tight fit is essential to the proper functioning of the respiratory protective device, makes an effective seal to the facial skin of the worker; and
(iv) if a tight fit is essential to ensure the worker is not exposed to one or more airborne contaminants to an extent that may pose a risk of significant harm to the worker, has been fit‑tested by a competent person in an approved manner;
(b) ensure that the respiratory protective device is regularly cleaned and maintained in an approved manner; and
(c) ensure that the respiratory protective device is kept, when not in use, in a convenient and sanitary location in which the respiratory protective device is not exposed to extremes of temperature or to any contaminant that may inactivate the respiratory protective device.
(2) If a respiratory protective device as required by subsection (1) is provided to a worker, the employer or contractor shall ensure that the worker:
(a) has been trained by a competent person in the proper testing, maintenance, use and cleaning of the respiratory protective device and in its limitations;
(b) can demonstrate that the worker:
(i) understands the training provided pursuant to clause (a);
(ii) can test, maintain and clean the respiratory protective device; and
(iii) can use the respiratory protective device safely;
(c) tests the respiratory protective device before each use;
(d) is assessed according to an approved standard as being capable of wearing a respiratory protective device; and
(e) is adequately informed respecting the reasons for the assessment required pursuant to clause (d).
(3) An employer or contractor shall ensure that the training required by clause (2) (a) includes practical experience by the worker in an uncontaminated environment.
(4) If respiratory protective devices are used only for emergency purposes, an employer or contractor shall ensure that a worker who may be required to use a respiratory protective device is given semi‑annual refresher training in its safe use.
(5) An employer shall ensure that the following records are kept as long as the worker who was provided with a respiratory protective device is employed by the employer and that the following records are made readily available for inspection and examination by the committee or the representative, as the case may be:
(a) records respecting fit‑testing for each worker that is completed pursuant to subclause (1) (a) (iv);
(b) records respecting the results of assessments for each worker that are completed pursuant to clause (2) (d);
(c) records respecting training completed by each worker pursuant to subsections (2) and (3).
(6) An employer shall ensure that any records mentioned in clause (5) (b) respecting a worker that are made available for inspection and examination pursuant to subsection (5) do not disclose any personal health information as defined in The Health Information Protection Act respecting the worker, unless the worker agrees to that disclosure.
(7) An employer shall ensure that records respecting the maintenance of atmosphere‑supplying respirators are kept and made readily available for inspection and examination by the committee or the representative as long as the worker who was provided with an atmosphere‑supplying respirator is employed by the employer.
(8) A worker may, at any time, inspect and examine any records kept pursuant to subsection (5) or (7) that relate to the worker.
Inspection of respiratory protective devices
7‑4. An employer or contractor shall ensure that:
(a) any respiratory protective device for emergency use is thoroughly inspected by a competent person at least once a month and after each use;
(b) the date of every inspection made pursuant to clause (a) and the name of the person who made the inspection are recorded and conspicuously displayed at the location where the respiratory protective device is stored; and
(c) any defects identified during the inspection carried out pursuant to clause (a) are corrected immediately by a competent person.
Inspection of full body harness, etc.
7‑21(1). If the use of a connecting linkage, personal fall arrest system, full‑body harness or lifeline is required by these regulations, an employer or contractor shall ensure that a competent person:
(a) inspects the connecting linkage, personal fall arrest system, full‑body harness or lifeline:
(i) as recommended by the manufacturer; and
(ii) after the connecting linkage, personal fall arrest system, full‑body harness or lifeline has sustained a fall‑arresting incident; and
(b) determines whether the connecting linkage, personal fall arrest system, full‑body harness or lifeline is safe for continued use.
(2) An employer or contractor shall ensure that a worker inspects the connecting linkage, personal fall arrest system, full‑body harness or lifeline before each use and that if a defect or unsafe condition that may create a hazard to a worker is identified in a connecting linkage, personal fall arrest system, full‑body harness or lifeline:
(a) steps are taken immediately to protect the health and safety of any worker who may be at risk until the defect is repaired or the unsafe condition is corrected; and
(b) as soon as is reasonably practicable, the defect is repaired or the unsafe condition is corrected.
PART 9
Safeguards, Storage, Warning Signs and Signals
Fall protection plan
9‑3(1). An employer or contractor shall develop a written fall protection plan if:
(a) a worker may fall 3 metres or more; and
(b) workers are not protected by a guardrail or similar barrier.
(2) The fall protection plan required by subsection (1) must describe:
(a) the fall hazards at the worksite;
(b) the fall protection system to be used at the worksite;
(c) the procedures used to assemble, maintain, inspect, use and disassemble the fall protection system; and
(d) the rescue procedures to be used if a worker falls, is suspended by a personal fall arrest system or safety net and needs to be rescued.
(3) The employer or contractor shall ensure that a copy of the fall protection plan is readily available before work begins at a worksite if a risk of falling exists.
(4) The employer or contractor shall ensure that a worker is trained in the fall protection plan and the safe use of the fall protection system before allowing the worker to work in an area where a fall protection system must be used.
Building shafts
9‑14(1). An employer, contractor or owner shall ensure that a work platform that is an integral part of a slip form used in a building shaft is designed by a professional engineer to withstand the maximum foreseeable load and is constructed, erected and used in accordance with that design.
(2) An employer, contractor or owner shall ensure that a platform mentioned in subsection (1) that has been moved is examined by a competent person and that a written report of the examination is made by the person who carried it out and kept by the employer, contractor or owner.
(3) An employer, contractor or owner shall not require or permit a worker to work on a platform mentioned in subsection (1) that has been moved before the platform has been examined in accordance with subsection (2), unless the worker is using a personal fall arrest system, a full‑body harness, a lanyard or a lifeline that meets the requirements of Part 7.
(4) If there is no work platform installed at the level of a doorway or opening in a building shaft, an employer, contractor or owner shall ensure that the doorway or opening is covered by a solid barrier that extends from the bottom of the doorway or opening to a height of at least 2 metres and is capable of preventing a worker or loose material from falling down the shaft.
(5) An employer, contractor or owner shall ensure that at least 1 warning sign indicating the presence of an open building shaft is placed on a barrier erected pursuant to subsection (4).
PART 10
Machine Safety
Explosive-actuated fastening tools
10‑10(1). In this section, "explosive‑actuated fastening tool" means a machine that propels or discharges, by means of an explosive force, a fastening device to attach the fastening device on, affix the fastening device to or cause the fastening device to penetrate another object or material.
(2) An employer or contractor shall ensure that a worker who operates explosive‑actuated fastening tool systems is trained in and uses safe work procedures for any explosive‑actuated fastening tool that the worker may operate, including:
(a) the selection of the appropriate tool, accessories, fastener and power load for each application;
(b) the limitations of each type of tool, fastener and power load; and
(c) the maintenance, inspection and use of the tool.
(3) An employer or contractor shall ensure that a worker who operates an explosive actuated fastening tool:
(a) does not leave the tool or explosive charges unattended;
(b) stores the tool and explosive charges in a locked container when not in use; and
(c) uses an industrial eye or face protector that meets the requirements of Part 7.
PART 11
Powered Mobile Equipment
Visual inspection
11‑3(1). Before a worker starts any powered mobile equipment, an employer or contractor shall ensure that the worker makes a complete visual inspection of the equipment and the surrounding area to ensure that no worker, including the operator, is endangered by the start‑up of the equipment.
(2) No worker shall start any powered mobile equipment until the inspection required by subsection (1) is completed.
Inspection and maintenance
11‑4. An employer or contractor shall ensure that:
(a) all powered mobile equipment is inspected by a competent person for defects and unsafe conditions as often as is necessary to ensure that it is capable of safe operation;
(b) if a defect or unsafe condition that may create a hazard to a worker is identified in the powered mobile equipment:
(i) steps are taken immediately to protect the health and safety of any worker who may be at risk until the defect is repaired or the unsafe condition is corrected; and
(ii) as soon as is reasonably practicable, the defect is repaired or the unsafe condition is corrected; and
(c) a written record of the inspections and maintenance carried out pursuant to clauses (a) and (b) is kept at the place of employment and made readily available to the operator.
Construction, repair, etc., of powered mobile equipment
11‑6. An employer, contractor, owner or supplier shall ensure that each unit of powered mobile equipment is constructed, structurally repaired, inspected, tested, maintained and operated in accordance with the manufacturer’s specifications or an approved standard.
PART 12
Scaffolds, Aerial Devices, Elevating Work Platforms and Temporary Supporting Structures
Scaffold planks and platforms
12‑7(1). An employer or contractor shall ensure that scaffold planks:
(a) are inspected by a competent worker to ensure that the scaffold planks are free of defects before the planks are incorporated in a scaffold;
(b) subject to subsections (2) and (4), are of 38 x 240 millimetre, number 1 structural grade spruce lumber or material of equivalent or greater strength;
(c) are the same thickness as adjoining planks;
(d) are laid tightly side by side with adjoining planks to cover the full width of the platform;
(e) are secured to prevent accidental or inadvertent movement in any direction;
(f) if wooden, do not span more than 3 metres between vertical supports on a light‑duty scaffold or 2.1 metres between vertical supports on a heavy‑duty scaffold;
(g) if metal or manufactured laminate, do not have a span between vertical supports greater than the span recommended by the manufacturer; and
(h) do not extend less than 150 millimetres or more than 300 millimetres beyond the bearers.
(2) An employer, contractor or supplier may use a manufactured scaffold plank if the plank is used according to the manufacturer’s recommendations and the manufactured scaffold plank is clearly marked with its maximum working load or the load specifications are readily available at the worksite.
(3) Subject to subsection (4), an employer or contractor shall ensure that a scaffold platform:
(a) is at least one‑half metre wide in the case of a light‑duty scaffold;
(b) is at least 1 metre wide in the case of a heavy‑duty scaffold; and
(c) is level or, if used as a ramp, has a slope at an angle not steeper than 5 horizontal to 1 vertical.
(4) A single manufactured extending painter’s plank, or a plank that is 51 x 305 millimetre, number 1 structural grade spruce lumber or material of equivalent or greater strength, may be used in a ladderjack scaffold.
Metal scaffolds
12‑9(1). If a metal scaffold is used, an employer or contractor shall ensure that the metal scaffold is:
(a) erected, used, maintained and dismantled in accordance with the manufacturer’s or professional engineer’s specifications and recommendations; and
(b) inspected, by a competent person, before use and daily when in use for any damage, deterioration or weakening of the scaffold or the scaffold’s components.
(2) If a metal scaffold or a component of a metal scaffold is damaged, deteriorated or weakened so that the strength or stability of the scaffold is affected, an employer or contractor shall ensure that the scaffold is not used until the scaffold or component is repaired or replaced by a competent person in accordance with the manufacturer’s or a professional engineer’s specifications and recommendations.
(3) If a metal scaffold is a tube and clamp scaffold, an employer or contractor shall ensure that:
(a) joints in adjacent uprights are staggered and do not occur in the same tier;
(b) joints in uprights are located not more than one‑third of a tier away from the connection of a ledger;
(c) ledgers are erected horizontally along the length of the scaffold and coupled to each upright at regular intervals of 1 tier;
(d) all ledgers are joined to form a continuous length;
(e) individual tube lengths of a ledger are the lesser of:
(i) 2 or more bays in length; or
(ii) the horizontal length of the scaffold;
(f) tubes of different metals or gauges are not joined together; and
(g) if base plates are required, they are securely installed in the uprights and securely attached to the sills.
(4) If a metal scaffold is a standard tubular frame scaffold, an employer or contractor shall ensure that:
(a) if base plates, shore heads, extension devices or screwjacks are necessary, they are securely installed and securely attached to the sills and the legs of the frame; and
(b) there are no gaps between the lower end of 1 frame and the upper end of the frame below on stacked frames.
(5) If a metal scaffold is a modular scaffold, an employer or contractor shall ensure that:
(a) if extension devices or screwjack bases and base collars are necessary, they are securely installed and securely attached to the sills;
(b) joints in adjacent uprights are staggered and do not occur in the same tier;
(c) there are no gaps between the lower end of 1 upright and the upper end of the upright below it;
(d) ledgers, bearers and braces are properly secured; and
(e) components from different modular scaffold systems are not used in the same scaffold.
Suspended scaffolds
12‑16(1). If a suspended scaffold is used, an employer, contractor or supplier shall ensure that the scaffold is:
(a) designed by a professional engineer and erected, used, maintained and dismantled in accordance with that design; or
(b) commercially manufactured to meet the requirements of an approved standard and erected, used, maintained and dismantled in accordance with the manufacturer’s specifications and recommendations.
(2) An employer or contractor shall ensure that the working parts of the hoisting mechanism of a suspended scaffold are left exposed so that defective parts or irregular working of the mechanism can be easily detected.
(3) An employer or contractor shall ensure that no worker is required or permitted to operate the hoisting mechanism of a suspended scaffold unless the worker is competent and has been designated by the employer or contractor to perform that work.
(4) An employer or contractor shall ensure that all parts of a suspended scaffold are inspected before use and daily when in use.
Use of suspended powered scaffolds
12‑19(1). An employer or contractor shall:
(a) develop work practices and procedures for the safe use of any suspended powered scaffold;
(b) train the workers in the procedures required pursuant to clause (a); and
(c) ensure that every worker complies with the procedures required pursuant to clause (a).
(2) An employer or contractor shall ensure that a suspended powered scaffold is operated by a competent worker.
(3) An employer or contractor shall ensure that all parts of a suspended powered scaffold are inspected before use and daily when in use.
(4) An employer or contractor shall ensure that a worker who works on a suspended powered scaffold is provided with and uses a full‑body harness, connecting linkage, personal fall arrest system and lifeline that meet the requirements of Part 7.
Workers' responsibilities
12‑20(1). Before starting to work on a suspended powered scaffold, a worker shall inspect the scaffold to ensure that:
(a) the thrustouts or parapet hooks are secured; and
(b) the suspension ropes and lifelines are free from abrasion or other damage.
(2) While working on a suspended powered scaffold, a worker shall:
(a) remain on the platform between the suspension ropes at all times;
(b) secure from fouling all ropes from the scaffold that extend to the ground or a landing;
(c) use a full‑body harness, connecting linkage, personal fall arrest system and lifeline that meet the requirements of Part 7; and
(d) ensure that, when the scaffold is being moved up or down on a suspension rope, the scaffold is kept level.
(3) A worker shall not:
(a) bridge the distance between a suspended powered scaffold and any other scaffold with planks or by any other means; or
(b) use the lifeline or the suspension ropes as a means of access to or exit from the scaffold except in cases of emergency.
(4) A worker shall comply with the work practices and procedures developed pursuant to clause 12‑19(1) (a).
Rolling scaffolds
12‑21(1). An employer or contractor shall ensure that the height of a rolling scaffold is not more than 3 times:
(a) the smallest dimension of the scaffold’s base; or
(b) if outriggers are provided, the smallest dimension of the scaffold’s base, including the extended outriggers.
(2) If outriggers are provided on a rolling scaffold, an employer or contractor shall ensure that the outriggers are firmly attached to the scaffold uprights to ensure the stability of the scaffold.
(3) An employer or contractor shall ensure that:
(a) each wheel on a rolling scaffold is equipped with a device to securely attach the wheel to the scaffold;
(b) if vertical adjusting devices are required, they are securely attached to the scaffold; and
(c) each rolling scaffold is secured against inadvertent movement while a worker is on the scaffold.
(4) An employer or contractor shall ensure that a scaffold erected on a movable platform is securely fastened to that platform.
(5) An employer or contractor shall not require or permit a worker to remain on a rolling scaffold while the scaffold is being moved unless:
(a) the height of the work platform does not exceed twice the shortest base dimension of the scaffold;
(b) the route to be travelled by the rolling scaffold has been thoroughly examined and found to be free of any condition that could cause the rolling scaffold to tilt or otherwise go out of control; and
(c) a work platform fills the entire area enclosed by the scaffold structure.
Maintenance and inspection
12‑26(1). An employer, contractor, owner or supplier shall ensure that only competent persons maintain and inspect an aerial device, elevating work platform, suspended powered platform, personnel lifting unit or scaffold to which section 12‑10 applies.
(2) An employer, contractor, owner or supplier shall ensure that a maintenance and inspection record tag:
(a) is provided for an aerial device, elevating work platform, suspended powered scaffold, personnel lifting unit or scaffold to which section 12‑10 applies, and is attached to the device, platform, unit or scaffold near the operator’s station; and
(b) has the following recorded on it:
(i) the date of the last maintenance;
(ii) the name and signature of the person who performed the maintenance; and
(iii) an indication that the maintenance has been carried out in accordance with the manufacturer’s recommendations.
Temporary supporting structures
12‑28(1). An employer or contractor shall ensure that a temporary supporting structure is designed and constructed to withstand safely all loads that the structure is intended, or may reasonably be anticipated, to support.
(2) Without limiting the generality of subsection (1), an employer or contractor shall meet the requirements of subsection (3) if a temporary supporting structure consists of:
(a) shoring that is more than 3.6 metres high; or
(b) members that are connected to one another so that a load applied to any member of the structure may alter the stresses induced in the other members.
(3) An employer or contractor shall ensure that:
(a) a temporary supporting structure mentioned in subsection (2):
(i) is designed by a professional engineer;
(ii) is inspected by a professional engineer after assembly and before use; and
(iii) is certified by a professional engineer to be safe; and
(b) all the drawings and other instructions necessary to construct and use the temporary supporting structure safely are kept at the worksite.
(4) An employer or contractor shall ensure that a scaffold constructed as an integral part of a temporary supporting structure is designed and certified to be safe by a professional engineer.
PART 13
Hoists, Cranes and Lifting Devices
Adoption of standards
13‑4(1). An employer or contractor shall ensure that all hoists, cranes and lifting devices manufactured on and after December 4, 1996 are constructed, inspected, tested, maintained and operated in accordance with an approved standard.
(2) A supplier shall ensure that all hoists, cranes and lifting devices manufactured on and after December 4, 1996 are constructed, inspected, tested and maintained in accordance with an approved standard.
Raising and lowering workers
13‑9(1). If a crane or hoist will be used to raise or lower workers, the employer or contractor shall:
(a) develop and implement work practices and procedures that will provide for the safe raising and lowering of the workers;
(b) train the workers in those work practices and procedures;
(c) ensure that the hoisting equipment and personnel lifting unit are inspected by a competent person before use and daily when in use; and
(d) ensure that the competent person records the details of the inspection in the log book.
(2) An employer or contractor shall not require or permit the operator of a crane or hoist to use the crane or hoist to raise or lower workers unless:
(a) the personnel lifting unit meets the requirements of subsection 12‑25(1);
(b) the suspension members of the personnel lifting unit are securely attached to the crane, hoist line or hook by a shackle, weldless link, ring or other secure rigging attachment;
(c) there is a secondary safety device that attaches the suspension members of the personnel lifting unit to the crane or hoist rigging above the point of attachment mentioned in clause (b);
(d) the load line hoist drum has a system or device on the power train, other than the load hoist brake, that regulates the lowering rate of speed of the hoist drum mechanism; and
(e) workers in the personnel lifting unit use a full‑body harness attached to the personnel lifting unit.
(3) An operator of a crane or hoist shall not use the crane or hoist to raise or lower workers unless:
(a) the personnel lifting unit meets the requirements of section 12‑25;
(b) the suspension members of the personnel lifting unit are securely attached to the crane, hoist line or hook by a shackle, weldless link, ring or other secure rigging attachment;
(c) there is a secondary safety device that attaches the suspension members of the personnel lifting unit to the crane or hoist rigging above the point of attachment mentioned in clause (b);
(d) the load line hoist drum has a system or device on the power train, other than the load hoist brake, that regulates the lowering rate of speed of the hoist drum mechanism; and
(e) workers in the personnel lifting unit use fall‑arrest protection attached to the personnel lifting unit.
Determining weight of load
13‑10(1). An employer or contractor shall provide the operator of a hoist, crane or lifting device with all the information necessary to enable the operator to determine readily and accurately the weight of any load that the operator is required or permitted to raise.
(2) An employer or contractor shall provide a permanent load gauge for a mobile crane that may be used for load ratings of 9 tonnes or greater at the minimum operating radius.
(3) A permanent load gauge required by subsection (2) must measure the weight of any load being hoisted and instantaneously indicate that weight to the operator.
(4) Subsection (2) does not apply to cranes that:
(a) use a device suspended by a wire rope to demolish a structure;
(b) use a magnet to raise or lower a load; or
(c) use a clam‑style load carrier to move material.
(5) An employer or contractor shall not require or permit a worker to use a crane mentioned in subsection (2) unless the crane is equipped with a permanent load gauge that will measure the weight of any load being hoisted and instantaneously indicate that weight to the operator.
(6) An employer or contractor shall ensure that:
(a) a worker who is required or permitted to use a crane equipped with a permanent load gauge is trained in the safe use and limitations of the permanent load gauge; and (b) the permanent load gauge is regularly inspected, maintained and calibrated in accordance with the manufacturer’s instructions.
Overload switches
13‑11(1). An employer, contractor or supplier shall ensure that a tower crane is equipped with:
(a) both:
(i) an overload limit switch that causes the hoist drum to stop when the load being hoisted exceeds the maximum rated load for any radius or boom angle or when the overturning moment exceeds the rated load moment; and
(ii) a moment overload switch that automatically restricts the radius within which the load can travel; or
(b) a permanent load gauge.
(2) An employer or contractor shall not require or permit a worker to use a tower crane unless:
(a) the crane is equipped with the overload limit switch and moment overload switch required by clause (1) (a) or the permanent load gauge required by clause (1) (b);
(b) the worker is trained in the safe use and limitations of the overload limit switch and the moment overload switch or the permanent load gauge; and
(c) the overload limit switch and moment overload switch or the permanent load gauge are regularly inspected, maintained and calibrated in accordance with the manufacturer’s instructions.
Log book
13‑17(1). An employer or contractor shall:
(a) provide a log book for each hoist and crane with a rated load greater than 5 tonnes and ensure that the log book is kept readily available;
(b) provide a copy of the log book to the operator on request;
(c) ensure that the hours of service of the hoist or crane and all details of any inspection, maintenance or calibration required by this Part are recorded in the log book;
(d) ensure that each entry required by clause (c) is signed by the person who performs the inspection, maintenance or calibration; and
(e) review and sign the log book on a regular basis.
(2) If the supplier of a hoist or crane provides a log book, an employer or contractor shall ensure that the information and signatures required by subsection (1) are recorded in the supplier’s log book instead of the employer’s or contractor’s log book and that the supplier’s log book is kept with the hoist or crane.
Inspections
13‑18(1). An employer, contractor or supplier shall ensure that a hoist, crane or lifting device is inspected by a competent person to determine whether the hoist, crane or lifting device is in safe working condition:’
(a) before the hoist, crane or lifting device is used at the start of each work shift; and
(b) at regular intervals as recommended by the manufacturer.
(2) If a defect or unsafe condition that may create a hazard to a worker is found in a hoist, crane, lifting device or rigging, an employer, contractor or supplier shall:
(a) take steps immediately to protect the health and safety of any worker who may be at risk until the defect is repaired or the unsafe condition is corrected; and
(b) as soon as is reasonably practicable, repair any defect or correct any unsafe condition.
(3) An employer, contractor or supplier shall ensure that a mobile crane is subjected to a thorough inspection, including non‑destructive testing, under the supervision of a professional engineer every 2 years or 1,800 hours of operation, whichever comes first.
(4) An employer, contractor or supplier shall ensure that a tower crane is subjected to a thorough inspection, including non‑destructive testing, under the supervision of a professional engineer:
(a) before erection at each site; and
(b) at subsequent intervals of 2,000 operating hours or 1 year, whichever occurs first.
(5) No worker shall operate a crane or cause a crane to be operated unless a copy of the results of the testing or inspection required by subsection (3) or (4) is readily available or is on site.
Repairs
13‑19(1). If the inspection of a hoist, crane or lifting device reveals a condition that might render the equipment unsafe or incapable of raising the rated load mentioned in subsection 13‑8(2), an employer, contractor or supplier shall not require or permit the use of the equipment until any necessary repairs are completed.
(2) An employer, contractor or supplier shall ensure that a structural repair or modification to a component of a hoist or crane is performed only under the direction and control of a professional engineer.
(3) Before a hoist or crane is used after a structural repair or modification, an employer, contractor or supplier shall ensure that:
(a) the equipment is tested under the direction of a professional engineer; and
(b) a professional engineer has determined the rated load of the repaired or modified hoist or crane and has certified that the hoist or crane is capable of safely raising the new rated load.
(4) If the rated load of a hoist or crane after repair or modification differs from the rated load before repair or modification, an employer, contractor or supplier shall ensure that a new indication of load rating is provided pursuant to section 13‑5.
Winches
13‑26(1). An employer or contractor shall inspect all manually‑operated hoisting or winching equipment thoroughly at appropriate intervals to ensure that the manually‑operated hoisting or winching equipment is capable of safe operation.
(2) Before a worker operates a winch on a vehicle, the worker shall ensure that the brakes are applied or other effective means are taken to prevent movement of the vehicle.
(3) A worker who operates a vehicle on which a winch is in use shall not move the vehicle until the winch operator has given a signal that the vehicle can be moved safely.
(4) An employer or contractor shall not require or permit a worker to cross over or under a winch cable between a winch and the load or to go underneath the load while a winch is in use.
Pile-driving equipment
13‑28(1). An employer or contractor shall ensure that:
(a) pile‑driving equipment is operated, inspected and maintained according to the manufacturer’s instructions; and
(b) any structural repairs or modifications to pile‑driving equipment are made under the direction of a professional engineer and certified as safe by the professional engineer before the pile‑driving equipment is put in service.
(2) If pile‑driving equipment is used, an employer or contractor shall ensure that a brake band or clutch that is contaminated by oil or grease is dismantled and cleaned or replaced before further use.
(3) An employer or contractor shall ensure that:
(a) before a pile is placed in position for driving, the pile head is cut square and, in the case of a timber pile, cleaned free of debris, bark and splintered wood; and
(b) workers are adequately protected from injury that may be caused by the failure of a pile being driven.
(4) An employer or contractor shall not require or permit a worker who works with pile‑driving equipment:
(a) to remain or ride on a load being moved;
(b) to work, stand or pass under a suspended load; or
(c) to be on the superstructure of the equipment or within range of a falling pile unless the worker is directly involved in the operation of hoisting piles.
(5) If a worker uses pile‑driving equipment, an employer or contractor shall ensure that:
(a) a pile hammer is securely chocked while the hammer is suspended and the equipment is not operating; and
(b) no pile is hoisted in the leads while a worker who is not directly involved in the operation is on the superstructure of the equipment or within range of a falling pile.
(6) If pile‑driving equipment is fitted with pressure hammers, an employer, contractor or supplier shall ensure that the hoses are equipped with safety chains or safety ropes on the pressure side of the hose connections.
(7) An employer or contractor shall ensure that:
(a) crane booms used with vibratory hammers or vibratory pile extractors are inspected monthly by a competent person for structural defects; and
(b) any structural defects found pursuant to clause (a) are repaired under the direction of a professional engineer and certified as safe by the professional engineer before the booms are put back into service.
(8) An operator of pile‑driving equipment shall ensure that:
(a) the pile hammer is securely chocked while the hammer is suspended and the equipment is not operating; and
(b) no pile is hoisted in the leads while a worker who is not directly involved in the operation is on the superstructure of the equipment or within range of a falling pile.
PART 14
Rigging
Inspection
14‑3. An employer or contractor shall ensure that all rigging and components of rigging are inspected thoroughly at appropriate intervals and visually inspected before use to ensure that the rigging and rigging components will safely perform the intended function of the rigging and rigging components.
Knots, wire rope clips
14‑8(1). An employer or contractor shall ensure that:
(a) no knot or wire rope clip is used as a stopper on a rope or rope end that passes through a winding drum; and
(b) no knot is used to connect rigging hardware to a wire rope.
(2) An employer or contractor shall ensure that all wire rope clips are:
(a) made of drop‑forged steel;
(b) installed according to the manufacturer’s instructions; and
(c) inspected at frequent intervals to ensure the nuts are tight.
(3) If U‑bolt clips are used to fasten wire rope, an employer or contractor shall ensure that:
(a) the U‑bolt is installed so that the U section bears on the short or dead end of the rope and the saddle bears on the long or live end of the rope;
(b) the nuts are correctly torqued; and
(c) the number of clips and the amount of rope turn‑back conform to the manufacturer’s specifications and instructions.
(4) If double saddle or fist clips are used to fasten wire rope, an employer or contractor shall ensure that the clips are installed in numbers and with the amount of rope turn‑back specified by the manufacturer.
(5) If double base clips are used to fasten wire rope, an employer or contractor shall ensure that the clips are at least 6 rope diameters in length.
PART 20
Diving Operations
Medical examination
20‑4(1). A diver must have a comprehensive medical examination conducted by a physician at least once every 12 months in accordance with the criteria set forth in Appendices A and B of Canadian Standards Association standard CAN/CSA‑Z275.2‑92 Occupational Safety Code for Diving Operations.
(2) No diver shall dive unless the diver has been certified by the physician mentioned in subsection (1) to be free of any medical condition that would make unsafe the performance of the type of dive to be carried out.
(3) A diver shall:
(a) provide the employer with a copy of the certificate mentioned in subsection (2); and
(b) place the original certificate in the diver’s personal log kept pursuant to section 20‑15.
(4) An employer shall:
(a) ensure that no diver is required or permitted to dive unless the diver provides the employer with a copy of the certificate mentioned in subsection (2) that has been obtained within the preceding 12 months;
(b) retain the copy of the certificate mentioned in clause (a) while the diver is employed by the employer; and
(c) ensure that every diver employed by the employer is competent in the use of any diving apparatus that the diver will be required to use in a diving operation.
Diving equipment
20‑10. An employer shall ensure that all diving equipment, including breathing apparatus, compressor, compressed gas cylinder, gas control valve, pressure gauge, reserve supply device, piping, helmet, winch, cable, diving bell or stage and every other accessory necessary for the safe conduct of the diving operation, is:
(a) of an approved design, sound construction, adequate strength and free from obvious defect;
(b) maintained in a condition that will ensure the equipment’s continuing operating integrity and suitability for the equipment’s use;
(c) adequately protected against malfunction at low temperatures that may be caused by ambient air or water or by the expansion of gas; and
(d) examined, tested, overhauled and repaired in accordance with the manufacturer’s recommended procedure.
General responsibilities of diver
20‑14. A diver shall:
(a) proceed in accordance with the general diving plan and the instructions of the diving supervisor;
(b) inspect the diver’s equipment immediately before each dive; and
(c) begin each dive by submerging and checking all equipment to ensure that there are no leaks and that the equipment is functioning properly.
PART 23
Asbestos
Inspection
23‑7(1). An employer, contractor or owner shall ensure that all friable asbestos‑containing material and all sprayed‑on asbestos surfaces are regularly inspected by the employer, contractor or owner and are inspected at least annually by a competent person to confirm that the material is not releasing, and is not likely to release, asbestos dust into the atmosphere.
(2) An employer, contractor or owner shall keep a written record of the annual inspection mentioned in subsection (1) and make a copy of the record available for reference by the workers.
Asbestos processes
23‑8(1) An employer or contractor shall:
(a) ensure that every asbestos process is carried out in a manner that prevents, to the extent that is practicable, the release into the air of asbestos dust;
(b) in consultation with the committee, develop an asbestos control plan that protects the health and safety of all workers in the event of the dispersal of asbestos dust into the atmosphere at a place of employment or worksite; and
(c) implement the asbestos control plan developed pursuant to clause (b).
(2) A plan developed pursuant to subsection (1) must be in writing and must include:
(a) the emergency procedures to be used in case of an uncontrolled release of asbestos, including:
(i) the means to protect exposed workers;
(ii) the methods to confine and control the release of asbestos; and
(iii) the decontamination procedures to be used;
(b) the asbestos processes that workers may undertake;
(c) the training of workers in any asbestos process the workers may be required or permitted to undertake;
(d) the methods to control the release of asbestos dust;
(e) the personal protective equipment that workers may be required to use;
(f) the decontamination procedures for:
(i) the worksite; and
(ii) the workers who undertake any asbestos process; and
(g) the inspection and maintenance schedule for all asbestos‑containing materials.
(3) An employer or contractor shall make a copy of the plan developed pursuant to subsection (1) readily available for reference by workers.
(4) If an asbestos process is undertaken, an employer, contractor or owner shall ensure that:
(a) the area is effectively isolated or otherwise enclosed to prevent the escape of asbestos dust to any other part of the place of employment;
(b) a warning notice is conspicuously displayed indicating that asbestos work is in progress;
(c) all asbestos‑containing materials removed are placed in appropriate receptacles that are impervious to asbestos and that are clearly labelled "Asbestos"; and
(d) the receptacles mentioned in clause (c) are handled and transported in a manner that will protect them from physical damage.
Ventilation equipment
23‑10(1). If exhaust ventilation equipment is used to contain asbestos dust, an employer, contractor or owner shall ensure that the equipment is:
(a) equipped with a HEPA filter;
(b) inspected regularly for defects;
(c) maintained; and (d) certified by a competent person at least once each year as being able to function safely and effectively.
((2) If exhaust ventilation equipment will exhaust into the interior of a place of employment that is occupied by workers, an employer, contractor or owner shall ensure that the equipment is tested in an approved manner by a competent person before beginning an asbestos process to ensure that the equipment is able to function safely and effectively.
Asbestos waste
23‑12(1). Subject to subsection (3), an employer or contractor shall ensure that asbestos waste or dust produced in a place of employment is cleaned away promptly, and at least once each day, by vacuum cleaning equipment equipped with a HEPA filter to prevent the escape of asbestos dust into the air or, if vacuum cleaning is not practicable, by wet methods.
(2) An employer or contractor shall ensure that the vacuum cleaning equipment mentioned in subsection (1):
(a) is inspected regularly for defects;
(b) is maintained; and
(c) is certified by a competent person at least once each year as being able to function safely and effectively.
(3) Subsection (1) does not apply to vacuum cleaning equipment used within an effectively isolated enclosure that is being used to control the release of asbestos dust.
(4) An employer or contractor shall ensure that workers who are employed in the disposal of asbestos wastes are adequately trained in the safe means of handling those wastes and the proper disposal of those wastes in a manner that will not create a hazard to the health or safety of workers at the disposal site.
Medical examinations
23‑16(1). In this section, "worker" means a worker who is regularly employed in an asbestos process.
(2) Not less than once every 2 years and with consent of the worker, the employer shall:
(a) offer to arrange for a medical examination of the worker during the worker’s normal working hours; and
(b) reimburse the worker for any part of the cost of the medical examination that the worker cannot recover.
(3) If a worker cannot attend a medical examination mentioned in subsection (2) during the worker’s normal working hours, an employer shall credit the worker’s attendance at the examination as time at work and ensure that the worker does not lose any pay or other benefits.
(4) A medical examination arranged pursuant to subsection (2) must include:
(a) a comprehensive medical history and physical examination with special attention to the respiratory system;
(b) lung‑function tests, including forced vital capacity and forced expiratory volume at 1 second; and
(c) any further medical investigations that are necessary for the diagnosis of an asbestos‑related disease.
PART 24
Silica Processes and Abrasive Blasting
Silica processes other than abrasive blasting
24‑6(1). If a silica process other than abrasive blasting is carried on, an employer or contractor shall ensure that the entry of dust into the air where workers may be present is prevented, to the extent that is practicable, by the provision of:
(a) total or partial enclosure of the process;
(b) efficient local exhaust ventilation;
(c) jets or sprays of a suitable wetting agent; or
(d) any other method that provides equivalent protection to the workers.
(2) An employer or contractor shall ensure that any enclosure, apparatus or exhaust‑ventilation equipment provided pursuant to subsection (1) is:
(a) maintained in accordance with subsections 6‑4(2) and (3);
(b) inspected daily when in use; and
(c) certified as safe and effective by a competent person at least once each year.
(3) An employer or contractor shall ensure that no air discharged from a ventilation system provided pursuant to subsection (1) is recirculated in the place of employment unless the air is passed through an effective dust removal system equipped with a device that will provide a warning to workers when the system is not working effectively.
Standards for blasting enclosures
24‑9(1) An employer or contractor shall ensure that every blasting enclosure is:
(a) constructed, operated and maintained to prevent the escape of dust;
(b) provided with an efficient, dust‑extraction system, that is operated continuously whenever the blasting enclosure is in use, whether or not abrasive blasting is actually taking place; and
(c) provided with efficient equipment for separating the abrasive from the dust, to the extent that is practicable.
(2) An employer or contractor shall ensure that an abrasive is not reintroduced into a blasting apparatus until the abrasive has been separated from the dust pursuant to clause (1) (c).
(3) An employer or contractor shall ensure that:
(a) a blasting enclosure is inspected daily when in use;
(b) a blasting enclosure, the equipment connected with the enclosure and the ventilating system associated with the enclosure are thoroughly examined and tested regularly by a competent person; and
(c) all defects identified pursuant to this section are remedied immediately.
(4) A competent person who carries out examinations and testing pursuant to clause (3) (b) shall record the results of those examinations and tests.
Medical examinations
24‑13(1). In this section, "worker" means a worker who is regularly employed in a silica process.
(2) Not less than once every 2 years and with consent of the worker, the employer shall:
(a) offer to arrange for a medical examination of the worker during the worker’s normal working hours; and
(b) reimburse the worker for any part of the cost of the medical examination that the worker cannot recover.
(3) If a worker cannot attend a medical examination mentioned in subsection (2) during the worker’s normal working hours, an employer shall credit the worker’s attendance at the examination as time at work and ensure that the worker does not lose any pay or other benefits.
(4) A medical examination arranged pursuant to subsection (2) must include:
(a) a comprehensive medical history and physical examination with special attention to the respiratory system;
(b) lung‑function tests, including forced vital capacity and forced expiratory volume at 1 second; and
(c) any further medical investigations that are necessary for the diagnosis of a silica‑related disease.
PART 25
Fire and Explosion Hazards
Fire extinguishers
25‑3(1). An employer, contractor or owner shall ensure that portable fire extinguishers are selected, located, inspected, maintained and tested so that the health and safety of workers at the place of employment is protected. (
2) An employer, contractor or owner shall ensure that portable fire extinguishers are placed not more than 9 metres away from:
(a) each industrial open‑flame portable heating device, tar pot or asphalt kettle that is in use; and
(b) each welding or cutting operation that is in progress.
PART 26
Explosives
Qualifications of workers
26‑2(1). An employer or contractor who plans to conduct blasting activities shall ensure that a worker who is to undertake a blasting operation:
(a) has been thoroughly trained in:
(i) the estimation of the amount of explosives required, and in placing, priming and initiating the charge;
(ii) the appropriate procedures to be followed to ensure the safety of other workers;
(iii) the procedures to be followed in the event of a misfire; and
(iv) the examination of the site after blasting to ensure that it is safe to return to the site;
(b) has demonstrated competence to carry out the procedures mentioned in clause (a);
(c) has a thorough knowledge of all federal and provincial statutes, regulations and codes of practice pertaining to the safe use of explosives that are relevant to the blasting operation in question; and
(d) holds a written authorization to blast signed by the worker’s employer.
(2) A worker shall not undertake a blasting activity until the worker possesses written authorization to blast signed by the worker’s employer.
PART 29
Oil and Gas
Daily tour book
29‑4. An employer, contractor or owner shall:
(a) provide for each rig a daily tour book and ensure that the book is kept at the site of the rig;
(b) ensure that all details of any inspection required by this Part, any repair made and all work activities undertaken at the site of the rig are recorded in the daily tour book;
(c) ensure that the record required by clause (b) is signed by the worker who performs the inspection; and
(d) ensure that the supervisor reviews the entries for the day in the tour book and signs the tour book daily.
Routine inspections
29‑5(1). An employer, contractor or owner shall ensure that a rig is inspected by a competent person before commencing operations and at least every 30 working days after that.
(2) If a defect or unsafe condition is identified during an inspection, an employer, contractor, owner or supplier shall ensure that:
(a) steps are taken immediately to protect the health and safety of any worker who may be at risk until the defect is repaired or the unsafe condition is corrected; and
(b) as soon as is reasonably practicable, any defect is repaired and any unsafe condition is corrected.
Raising and lowering derricks
29‑9(1). Before a derrick is raised or lowered, an employer, contractor or owner shall ensure that a complete inspection of all of the derrick’s parts is made by a competent person.
(2) An employer, contractor or owner shall ensure that:
(a) a competent person is in charge of, and present during, the raising and lowering of a derrick; and
(b) a derrick is raised or lowered in accordance with the manufacturer’s specifications.
Means of escape
29‑13(1). An employer, contractor or owner shall ensure that a derrick is equipped with a specially rigged and securely anchored auxiliary escape line that provides a ready, safe and convenient means of escape from the fourble board and the crown in the derrick.
(2) An escape line required by subsection (1) must be a wire rope with a minimum diameter of 11.5 millimetres and must be installed with a safety buggy that is equipped with a braking device.
(3) An employer, contractor or owner shall ensure that:
(a) the tension on an escape line is sufficient to ensure that a worker descending the escape line can stop 6 metres from the ground anchor point;
(b) an escape line is clearly marked and protected from physical damage;
(c) an escape line is visually inspected by a competent person at least once a week; and
(d) a path of escape is kept free of obstruction.
(4) An employer, contractor or owner shall ensure that no worker is required or permitted to slide down a pipe, tube, rod, kelly, cable or rope line on a derrick except in an emergency.
Pressure relief devices
29‑16(1). An employer, contractor, owner or supplier shall ensure that every drilling fluid pump and servicing fluid pump is equipped with a pressure relief device in accordance with this section.
(2) A pressure relief device must be installed on the discharge side of a positive displacement drilling fluid pump or servicing fluid pump.
(3) There must not be a valve between a drilling service pump or servicing fluid pump and a pressure relief device.
(4) A pressure relief device must be set to discharge at a pressure not in excess of the maximum working pressure for which the drilling fluid pump or servicing fluid pump and the connecting pipes and fittings have been designed.
(5) A pressure relief device and its components must be of a design and strength specified in the manufacturer’s design specifications for the pressure relief device.
(6) An employer, contractor or owner shall ensure that fluids or materials discharged through a pressure relief device are piped to a place where they will not endanger workers.
(7) The diameter of piping connected to the pressure side and discharge side of a pressure relief device must not be smaller than the diameter of the openings to the device.
(8) The piping on the discharge side of a pressure relief device must be:
(a) secured to prevent movement; and
(b) sloped to drain fluids away from the discharge outlet.
(9) A mud gun used for jetting must be securely anchored.
(10) Valves of the quick closing type must not be used on the discharge line from a drilling fluid pump or servicing fluid pump.
(11) An employer, contractor or owner shall ensure that a drilling fluid pump or servicing fluid pump is protected against freezing.
(12) An employer, contractor or owner shall ensure that a fluid pump using a pressure relief device is routinely inspected by a competent person to ensure the pressure relief device is in good operating condition.
Spudding in
29‑18. An employer, contractor or owner shall ensure that spudding in is not begun until:
(a) all safeguards required by these regulations are in place;
(b) all platforms, stairways, handrails and guardrails are installed and securely fastened in position; and
(c) the auxiliary escape line required by section 29‑13 is installed and inspected.
Drawworks
29‑23(1). An employer, contractor or owner shall ensure that the drawworks on every drilling rig is equipped with an automatic feed control.
(2) An employer, contractor or owner shall ensure, with respect to the drawworks on a rig, that:
(a) the mechanism installed or used to hold down the brakes in the engaged position is designed to prevent accidental disengagement;
(b) a competent person tests the brakes at the beginning of each shift and inspects the brakes at least weekly to ensure that they are in good working order; and
(c) controls are not left unattended while the hoist drum is in motion except during drilling.
PART 30
Additional Protection for Electrical Workers
Portable power cables and cable couplers
30‑8(1). An employer or contractor shall ensure that every portable power cable and cable coupler is:
(a) protected from physical or mechanical damage; and
(b) inspected by a competent person at intervals that are sufficient to protect the health and safety of workers.
(2) An employer or contractor shall ensure that:
(a) if any unsafe condition is identified in a portable power cable or cable coupler, the portable power cable or the cable coupler is repaired or taken out of service; and
(b) every splice in a portable power cable is sufficiently strong and adequately insulated to retain the mechanical and dielectric strength of the original cable.
(3) A worker shall take all reasonably practicable steps not to drive equipment over, or otherwise damage, a portable power cable or cable coupler.
PART 31
Additional Protection for Health Care Workers
Cytotoxic drugs
31‑5(1). In this section, "cytotoxic drugs" means drugs that inhibit or prevent the functions of cells and are manufactured, sold or represented for use in treating neoplastic or other conditions.
(2) An employer shall take all practicable steps to minimize the exposure of workers to cytotoxic drugs or to materials or equipment contaminated with cytotoxic drugs.
(3) If workers prepare parenteral cytotoxic drugs on a frequent and continuing basis, an employer shall provide and maintain an approved biological safety cabinet in accordance with subsection (4) and ensure that workers use the cabinet safely.
(4) A biological safety cabinet must be:
(a) inspected and certified by a competent person at least annually and when the biological safety cabinet is moved; and
(b) used and maintained according to an approved procedure or the manufacturer’s recommendations.
(5) If workers are required to prepare, administer, handle or use cytotoxic drugs or are likely to be exposed to cytotoxic drugs, an employer, in consultation with the committee, shall develop a written program to protect the health and safety of workers who may be exposed to cytotoxic drugs or to materials or equipment contaminated with cytotoxic drugs.
(6) A program developed pursuant to subsection (5) must include:
(a) the measures to be taken to identify, store, prepare, administer, handle, use, transport and dispose of cytotoxic drugs and materials contaminated with cytotoxic drugs;
(b) the emergency steps to be followed in the event of:
(i) a spill or leak of a cytotoxic drug; or
(ii) worker exposure to cytotoxic drugs by a puncture of the skin, absorption through the skin, contact with an eye, inhalation of drug dust or ingestion of a contaminated substance;
(c) the methods to be followed in maintaining and disposing of equipment contaminated with cytotoxic drugs;
(d) the use to be made of engineering controls, work practices, hygiene practices and facilities, approved respiratory protective devices, approved eye or face protectors and other personal protective equipment and decontamination materials and equipment that are appropriate in the circumstances; and
(e) the use to be made of an approved biological safety cabinet for the preparation of cytotoxic drugs and the methods to be followed in maintaining the cabinet.
(7) An employer shall:
(a) implement the program developed pursuant to subsection (5);
(b) ensure that all workers who may be exposed to cytotoxic drugs or to materials or equipment contaminated with cytotoxic drugs are trained in the program; and
(c) make a copy of the program readily available for reference by workers.
Equipment contaminated with waste
31‑7. An employer shall ensure that, if reasonably practicable, any equipment that has been contaminated with waste is inspected and decontaminated before it is repaired or shipped for repair.
Anaesthetic gases
31‑12. If workers are required to handle or use anaesthetic gases and vapours or are likely to be exposed to anaesthetic gases and vapours, an employer shall:
(a) develop safe work practices and procedures to eliminate or reduce the concentration of anaesthetic gases and vapours in the air of the room during the administration of the anaesthetic gases;
(b) train workers in the safe work practices and procedures developed pursuant to clause (a) and ensure that the workers and self‑employed persons use those safe work practices and procedures;
(c) ensure that all anaesthetic gas hoses, connections, tubing, bags and associated equipment are inspected for leakage before each use and at least weekly;
(d) ensure that any room where anaesthetic gases are administered is, if reasonably practicable, ventilated at a rate of 15 air changes per hour;
(e) install an effective waste anaesthetic gas scavenging system to collect, remove and dispose of waste anaesthetic gases and vapours;
(f) except in birthing rooms where anaesthetic gas is self‑administered, ensure that leakage from a waste anaesthetic gas scavenging system installed pursuant to clause (e) is less than 100 millilitres per minute when tested according to an approved standard; and
(g) ensure that the waste anaesthetic gas scavenging system and the equipment used to administer anaesthetic gases are maintained.
PART 32
Additional Protection for Firefighters
General standards for vehicles and equipment
32‑5. An employer, contractor or owner shall ensure that all firefighting vehicles and all equipment for use in emergency operations are designed, constructed, operated, maintained, inspected and repaired so as to protect adequately the health and safety of firefighters.
Inspection of firefighting vehicles and equipment
32‑7. An employer, contractor or owner shall ensure that:
(a) all firefighting vehicles and firefighting equipment are inspected by a competent person for defects and unsafe conditions as often as is necessary to ensure that the vehicles and equipment are capable of safe operation;
(b) if a defect or unsafe condition that may create a hazard to a firefighter is identified in a firefighting vehicle or firefighting equipment:
(i) steps are taken immediately to protect the health and safety of any firefighter who may be at risk until the defect is repaired or the unsafe condition is corrected; and
(ii) as soon as is reasonably practicable, the defect is repaired or the unsafe condition is corrected; and
(c) a written record:
(i) is kept of all inspections carried out pursuant to clause (a);
(ii) is signed by the competent person who performs the inspection; and
(iii) is kept at the place of employment and is made readily available to the committee, the representative and the firefighters.
Instructor-Led
Self-Directed
Instructor-Led
- Energy Safety Canada - Hazard Management
- Safety Association of Saskatchewan Manufacturers - Inspections
- Safety Association of Saskatchewan Manufacturers - OH&S Committee Level 1 & 2
- Saskatchewan Association for Safe Workplaces in Health - Inspections
- Service Hospitality – Workplace Inspections
Self-Directed
These forms do not replace the legislation. Please carefully review the Disclaimer on each form that you choose to use, and refer to the relevant legislation to find out exactly what requirements apply to your business. WorkSafe Saskatchewan assumes no responsibility or liability for the use of these forms, nor does WorkSafe Saskatchewan offer any advice as to your obligations under any applicable legislation.
CCOHS
- Effective Workplace Inspections
- Inspection Checklist- sample checklist for outdoor work areas
- Inspection Checklists
- Workplace Housekeeping- checklist for General Inspection
Safety Associations
- Energy Safety Canada, Petroleum Industry Safety Association
- Saskatchewan Association for Safe Workplaces in Health
- Saskatchewan Construction Safety Association
- Service Hospitality